It’s true: Boshart Industries no longer has a Quality Control department.
In fact, we haven’t had one since mid-2019.
How is that possible?
THE PROBLEM WITH QUALITY CONTROL
While it’s true we no longer have a Quality Control department, we’ll save you the suspense and clarify: we do have a Quality Assurance department that replaced it in mid-2019.
What’s the big difference between the two?
Most Quality Control departments—previously including ours—are passive in nature. They only begin looking for issues with product when there’s been significant customer feedback expressing dissatisfaction.
What’s worse about that is, in our experience, only a small fraction of customers that might be experiencing issues actually reach out, while the vast majority drop the product in favour of a new one in the future. Not only does the customer feel ripped-off having received a subpar product, the company responsible for that product is still distributing it.
The big issue in this instance is that the problem with the product is widespread and only addressed after it’s caused damage or become a headache for the end-user.
At Boshart, we never settle for being good enough, so the idea that we could be negligently putting bad product into circulation didn’t sit right with us, so we completely overhauled our process.
THE BENEFIT OF QUALITY ASSURANCE
As we said, we reformatted our Quality Control department to instead be focused on Quality Assurance. Other than a name change, what does this mean to our customers?
It means Boshart takes a far more active approach to ensuring the quality and consistency of every product we distribute. We don’t just wait for problems to arise: we actively go out seeking them before they become your problem.
By being proactive in this process, we significantly reduce the risk of distributing subpar product that would fail an inspection. We want to address the problem at the source.
OUR APPROACH TO QUALITY
While we can’t get into too many specifics on how certain products are tested (due to their relation to industry trade secrets), we can give you a brief look into our process.
Dual Sourcing
Currently, one of the primary goals in our Quality Assurance department is to secure dual sourcing for all products we distribute.
What this means is that we are not entirely dependent on a single supplier to provide our entire stock on a particular part.
The benefit to our customers: should we encounter a non-conformance (where a product does not meet our standards of quality), we have a backup that we can utilize in the meantime while we are working with the first supplier to solve the issues we’ve detected.
This keeps our supply chain strong and much more reliable, even when we encounter issues with our products. We are keen to reduce interruptions in our service wherever possible.
Daily Testing
We have a team that executes daily testing of a number of our products—both manufactured on-site and those produced abroad—ensuring things like our packaging is consistent, our metals contain the proper alloys that are allowed under specifications, our valves withstand maximum pressure ratings, and countless other tests to ensure our products not only match standards, but exceed them.
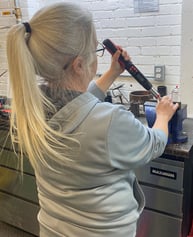
Some customers might expect that we would demonstrate favouritism to the products that we manufacture here at our facility in Milverton, Ontario, but in fact the opposite might be true. We are incredibly strict about our testing because we know that a quality end product is the most important thing we can provide our customers.
Even walking around the factory floor, many of our staff will tell you that testing is done more frequently than management expects them to. At Boshart, quality isn’t just an executive concern: it’s an initiative that everyone takes part in.
Certifications
Obtaining certifications on certain products is considerably more difficult than the average person realizes. It is a significant financial investment to have a product tested and certified to meet standards. In some circumstances, we have to work with our suppliers to reimagine their manufacturing process in order to guarantee that our standards of quality are met.
At Boshart, we have varying certifications on products with the following organizations:
- Underwriters Laboratories (UL)
- American Society for Testing & Materials (ASTM)
- National Sanitation Foundation (NSF)
- International Association of Plumbing & Mechanical Officials (IAPMO)
- American National Standards Institute (ANSI)
- American Society of Mechanical Engineers (ASME)
- American Society of Plumbing Engineers (ASPE)
- Canadian Standards Association (CSA)
- United States Environmental Protection Agency (EPA)
- And countless others.
When a Boshart product has two certifications from different governing bodies, we always test to the more strict standard between the two. This ensures that, no matter the circumstance, there is no confusion that our product will meet or greatly exceed performance expectations.
IN CONCLUSION
Boshart’s philosophy of quality assurance is something that runs deep in our company. It is not an initiative that has been devised and executed by a single department.
We never want to settle for being good enough. Industry leaders never tire of pushing the envelope further and further.
We are far from a perfect company. We aren’t here to say that there are never issues with our products.
But we wear our Quality Assurance protocols like a badge of honour, signifying that quality is of the utmost significance to us. In doing so, our customers know that anything bearing the Boshart name is a product they can trust. We’ve done the testing and hard work for them.
Have further questions about this subject?
Head over to Boshart's Knowledge Base: technical product information, guidelines, and more.
SHARE